Waterproofing issues can often be prevented with the simple stroke of a pen — that is, if we still used pens to design and draft. A thorough understanding of which waterproofing products to specify and how to properly detail waterproofing assemblies is a critical first step in the construction of a well-built, waterproofed building.
As Building Envelope Consultants, we routinely review construction documents and their waterproofing-related design components. Although this is similar to a “peer review,” there is a fundamental difference. We are focused on the entire building envelope — from below-grade to the roof, and every building “shell” element in between. Over the course of providing plan reviews for a great many years, we have developed a list of five common waterproofing design mistakes that we encounter on nearly every set of architectural drawings. Although the term “Building Envelope” (or “Building Enclosure”) refers to the exterior shell of a building, we are often tasked as waterproofing consultants with reviewing interior items as well. This can include such elements as showers, trash rooms, pump rooms, garage deck coatings, etc. However, for the sake of this article, we will stick to exterior considerations.
Our Building Envelope Group has also been heavily involved in “architectural forensics” — the examination of construction defects — which has provided us the benefit of studying how waterproofing assemblies fail, and how these failures can be avoided. We have found that this can be done, in part, by better communication through the design, detailing, and specification process.
In addition to potential inadequate detailing by the architect, many water-proofing failures are attributable to improper use of materials or incorrect installation during the construction phase. But, that is a subject for another article. For now, we will focus on what we can do as architects, designers, and building envelope professionals to make sure that these failures do not originate with the design and detailing of buildings.
There are many drafting conventions we encourage designers and draftspersons to implement when producing their documents, such as using a larger scale on details so that proper lapping of waterproofing layers can be clearly seen, and utilizing axonometric/3D details where possible.
In this article, we will address the most common design-related mistakes:
- Inadequate Roof Slopes
- Non-sloped Horizontal Substrates
- Improperly Designed Wood Framed Decks
- Ineffective Water Management in Exterior Stucco Finishes
- Poor Understanding the Hygrothermal Characteristics of Exterior Assemblies
1. Inadequate Roof Slopes
We are all familiar with the general building code standard of a minimum roof slope of quarter-inch per foot (1/4”/ft). What is commonly misunderstood (or at least not properly considered) is that if two 1/4”/ft. sloped roof planes intersect to form a valley, this valley will have a slope of substantially less than 1/4”/ft.
We invariably find ponding on such roofs at these valleys. Therefore, we always encourage designers to show primary and secondary (as with the use of crickets) roof plane slopes of at least 1/2”/ft. This will work toward making the valley slopes drain better. It can be a complicated math problem (well beyond Pythagorean’s Theorem) to figure out how steep all planes must be to get valleys to slope at a minimum of 1/4”/ft. But, suffice it to say that roof planes need to have a steeper slope than the code minimum in order to provide adequate drainage at valleys.

2. Non-sloped Horizontal Substrates
One design mistake we almost always encounter is the lack of provision for drainage slope in substrates that provide a base for the waterproofing and drainage plane. Most of the time, architects and designers assume that a sloped surface material is all that is needed for proper drainage. The problem is that topping slabs, tile grout, and other similar finish surface components are porous. So even though a sloped top surface will take care of a good portion of the initial “sheet” drainage, water ultimately finds its way down at the substrate level. If this level is not sloped as well, the water will simply remain there.
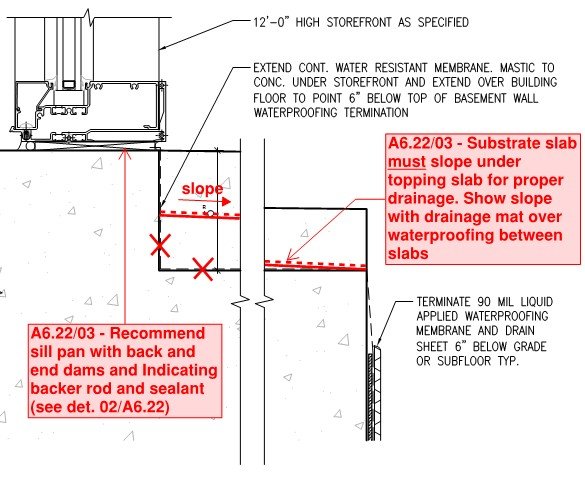

3. Improperly Designed Wood Framed Decks
Exterior wood framed decks and balconies can be especially problematic — even lethal. This was the case in 2015, when a severely water-damaged balcony collapsed in Berkeley, CA, resulting in the deaths of six young people. Some of the issues discussed here pertain also to metal and concrete decks, but due to the characteristics of wood (when used as a structural material) and its tendency to not fare well when exposed to inordinate amounts of water, we will set our focus on wood framed decks.
The slope of the deck for proper drainage is of paramount importance. Whether this drainage pattern leads to area drains or off the edge of the deck, water must not be allowed to “stand” (see Issue 2 above). Many wood decks are simply coated with a deck coating product. These coatings must be maintained and reapplied on a regular schedule for them to continue to protect the wood effectively.
Some wood decks have a more robust surface, such as concrete or tile, which requires a waterproofing membrane system between this surface and the plywood deck. In these “sandwiched” membrane systems, the membrane level needs a drain mat and transition flashings, much like at roof-to-wall conditions, to direct runoff away from the walls. The drainage plane must also have a method of discharging the water that makes it through the surface material. Oftentimes, no weep holes or other relief systems are provided, rendering the drainage plane ineffective.
Guardrail base plate anchorage to decks is also a source of many wood deck failures from water intrusion. The base plates are usually designed to sit on top of the deck sheathing, leading to irregularities in the waterproofing. One method is to “let in” or depress the base plates and bolts into the deck framing so that waterproofing can be laid over in a continuous plane. A more effective method, however, is to mount railings to the face of deck edges or to guardrail walls, thus eliminating holes in the horizontal deck system. (This item was done correctly in Figure 3.)
When decks and balconies are designed to be surrounded by low wall framing, scuppers are often used to drain decks. We often come across over complicated scuppers that lack the basic wall plane flashings on both sides of the wall, or scuppers in which the sheet metal is too thin (leading to deformation), too short, or lacks positive slope all the way out to a drip edge.
Proper flashing at the deck-to-wall junction is also a very critical component, no matter what the surface finish is. This protects the connection of the deck to the structure. Many times, this flashing is not properly executed at doorway thresholds. Details for this area must show how the deck flashing ties into a threshold pan and a “weather drop” (step down from interior to exterior) must be dimensioned.
4. Ineffective Water Management in Exterior Stucco Finishes
One issue that is almost never taken into consideration is water management in exterior finishes, especially stucco. This problem compounds the taller a structure is. We routinely suggest stucco breaks at floor lines, such as a Cemco M-Slide (see Figure 4).
These types of products allow water that has penetrated through the porous stucco to drain out at each floor line, instead of having to travel down the drainage plane to the bottom floor weep screed. This particular product also allows for the compression and movement of the structure as more and more weight is added on top of each platformed floor.
Not allowing water to drain out of a stucco wall system at frequent intervals can cause many problems, such as blistering, spalling, weather barrier deterioration, organic growth, and discoloration.
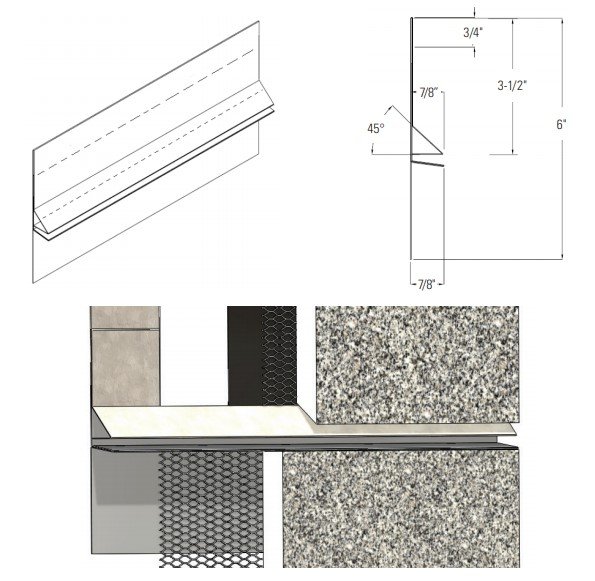
5. Poor Understanding the Hygrothermal Characteristics of Exterior Assemblies
Although it sounds complicated, the hygrothermal performance of an exterior assembly simply refers to the movement of heat and moisture through walls and roofs. A thorough understanding of at least the basics can help designers avoid assemblies that can cause a myriad of water-related problems.
As an example, in cold climates, the old rule of thumb for placement of moisture barriers was “warm side in winter.” While this may work in Vermont, this is not an ideal barrier placement in other climates. Improper placement of barriers in the envelope system can result in condensation where it is not wanted, causing problems such as organic growth (mold, mildew, etc.), wood rot, rust in metal components, and so on. A lot has been made recently of the thermal performance of enclosure systems, but these enhanced thermally efficient assemblies can cause other problems if the transfer of heat and moisture is not taken into account for the assembly and climate in which it is being built.
There are very sophisticated software programs on the market that will predict the hygrothermal performance of external assemblies, such as WUFI, a widely used German engineering software. Your Building Envelope Consultant can help you design the enclosure of your building for maximum performance and ensure that there will not be unintended water-related consequences.
Optimizing the Value of Your Building Envelope Consultant
We know architects have a million things to think about when designing a building — programming for the end user, zoning, allowable FAR, exiting, structural, MPE, Fire Codes, and now, “green” and enhanced energy efficiency/performance of structures. The requirement for exterior insulation alone has accounted for untold waterproofing problems. The Building Envelope Consulting industry was born as a result of these new and complicated requirements. Building Envelope Consultants should be viewed as any other consultant typically hired by architects. Not only can Building Envelope Consultants help during the design phases, but we can also help architects with other services such as waterproofing-related specifications, product, and shop drawing submittal reviews, RFI responses, construction phase observations and inspections, and more.
How Can VERTEX Help?
In our effort to add value to our architectural clients, VERTEX provides AIA CEU accredited training in which we discuss these and many other important issues relating to the Building Envelope. If you are an architect, contractor, or developer and could benefit from these educational sessions, please contact us.
To learn more about VERTEX’s Building Envelope Consulting services or to speak with a Construction Expert, call 888.2985162 or submit an inquiry.
Author: Kirk O’Brien AIA
This article was originally published by Xpera Group which is now part of The Vertex Companies, LLC.